Know the best practices for U.S. truck fleet maintenance
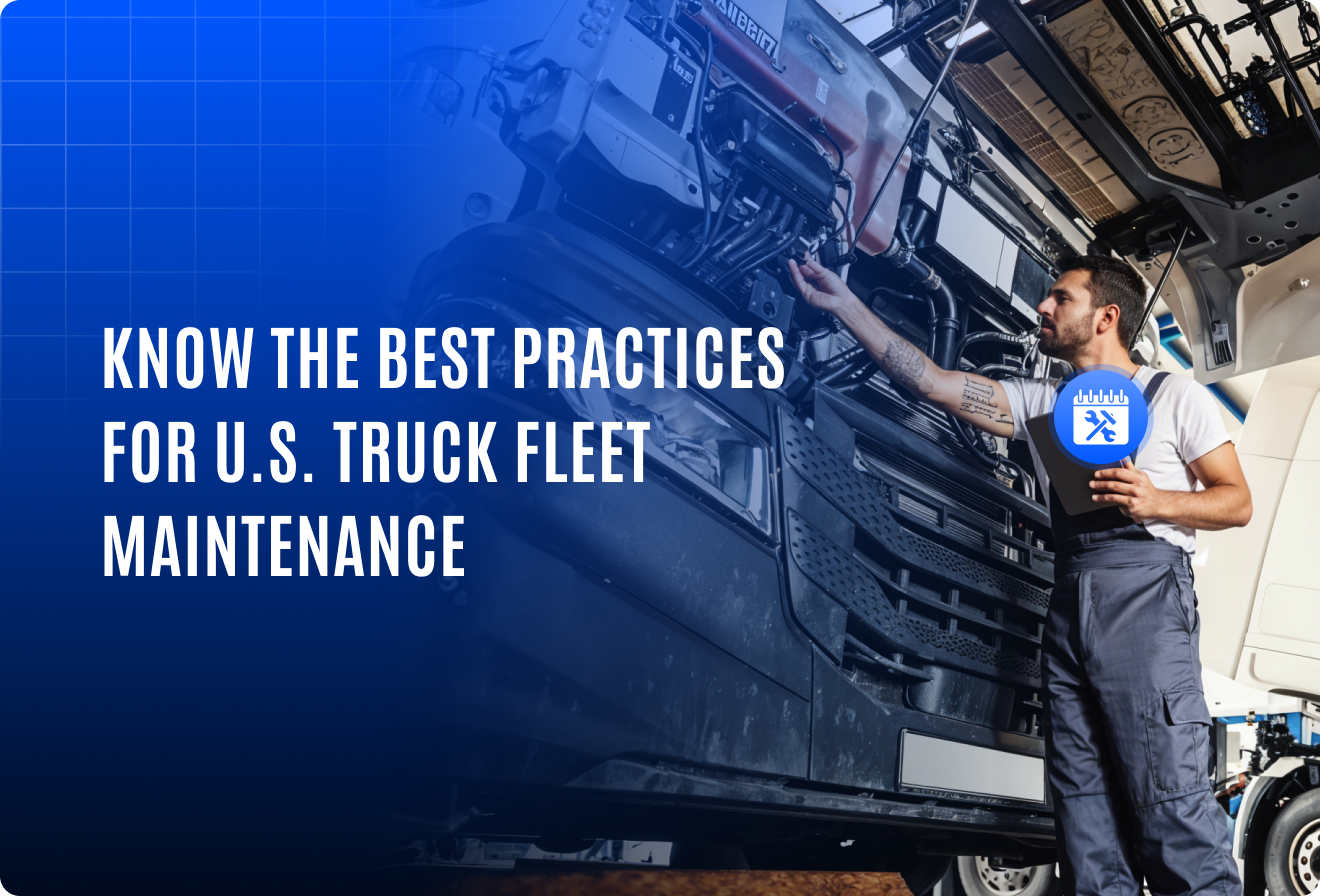
Truck fleets power the logistics network in the United States. From cross-country freight to last-mile delivery, trucks play a vital role in keeping businesses moving. According to the American Trucking Associations, trucks handle over 72 percent of all freight transported across the country. The industry also supports more than 8 million jobs. With over 13 million commercial trucks on the road, maintaining each vehicle is a major responsibility. Good fleet maintenance helps reduce breakdowns, ensures driver safety, and keeps fleets compliant with DOT(Department of Transportation) regulations. It also helps companies control costs and avoid delays. In this blog, you will learn about the best truck fleet maintenance practices that work well for U.S. businesses. These tips can help you improve operations, stay compliant, and manage your fleet more efficiently.
Key truck fleet maintenance practices for U.S. fleets
Maintaining a truck fleet takes more than just reacting when something goes wrong. It requires consistent care and smart planning. Here are some of the most important practices that U.S. fleet operators follow to keep their vehicles in top shape.
- Regular inspections and preventive care
Routine checks help you catch small problems before they turn into expensive repairs. In the U.S., the Department of Transportation requires regular vehicle inspections to ensure road safety. Keeping up with these not only avoids fines but also helps reduce breakdowns and improve uptime. - Tire pressure and wear checks
Tires take a beating, especially when trucks travel across different climates. Hot weather in the South and cold winters in the North both affect tire performance. Regularly checking tire pressure and tread depth can prevent blowouts and save fuel. - Engine and oil monitoring
Oil keeps your engine running smoothly. Ignoring oil changes or engine performance can lead to serious damage. Make sure every truck has a set schedule for oil changes and basic engine diagnostics. - Brake system inspections
Brakes are one of the most used parts of a truck, especially on steep or crowded routes. Worn-out brake pads or fluid issues can quickly turn into safety hazards. Regular brake checks help reduce risk and ensure better control on the road. - Battery and electrical system care
Truck batteries can drain faster in extreme temperatures. Whether your fleet operates in snowy states or high-heat regions, it is important to test battery life and inspect electrical components regularly to avoid unexpected failures. - Use digital tools and automation
Fleet maintenance software helps you track vehicle health, schedule services, and store inspection records. With fleets spread across states, having a central digital system avoids missed checkups and improves uptime.
Common maintenance challenges faced by U.S. fleets
Even with a good plan in place, U.S. fleet operators face many challenges when it comes to maintenance. These issues vary depending on the size of the fleet, the region, and the type of operation.
- Managing vehicles across multiple locations
Many fleets operate in more than one state. Each state may have its own inspection rules, climate conditions, and road quality. Keeping track of service schedules for trucks in different locations becomes difficult without a centralized system. - Unplanned breakdowns and emergency repairs
Even with regular checks, things can go wrong on the road. Breakdowns lead to missed deliveries and extra costs. For fleets that work on tight deadlines, emergency repairs can quickly disrupt operations. - Lack of real-time maintenance data
Without digital tools, managers often rely on paper logs or manual updates. This leads to delays in detecting problems and makes it harder to schedule repairs on time. - Difficulty in finding skilled technicians
There is a growing shortage of qualified technicians across the U.S. This makes it harder for fleet managers to get trucks serviced quickly, especially in remote or high-demand areas. - High cost of parts and services
Parts prices and labor rates have gone up in many parts of the country. If fleets are not tracking expenses or planning maintenance smartly, costs can pile up fast.
Smart maintenance solutions for U.S. fleets
To handle these challenges, U.S. fleet operators are turning to smarter systems and better planning. These solutions help reduce unplanned costs, improve safety, and keep vehicles running longer.
- Centralize all data with software
A digital platform brings together service logs, vehicle diagnostics, and alerts. This makes it easy to manage maintenance across locations and avoid paperwork delays. - Automate service reminders
Automatic alerts help you stay on top of oil changes, part replacements, and inspections. This reduces the risk of unexpected downtime. - Monitor vehicle health in real time
Modern tools can send instant alerts for issues like engine trouble or low tire pressure. This allows quick action before problems become serious. - Build a network of service partners
Fleets that operate in many regions benefit from having reliable garages on call. This cuts repair delays and ensures quality service everywhere. - Track maintenance spending
Keep an eye on costs with proper expense tracking. Knowing how much each vehicle costs over time helps with planning replacements or upgrades.
Conclusion
For U.S. fleets, truck fleet maintenance is not just about fixing problems. It is about staying ahead of them. With proper planning and the right tools, you can avoid costly delays, reduce breakdowns, and run a safer operation.
Strong maintenance practices keep your trucks moving, your drivers safe, and your business on track.